2 min read
Wood Manufacturer is 32% More Efficient from a Simple Software Integration
Admin May 22, 2019
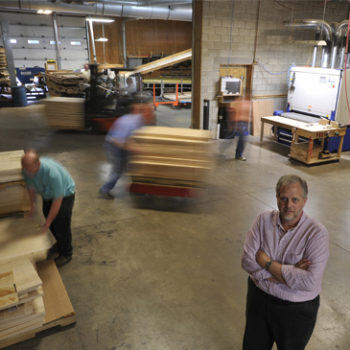
Tilo Industries is a family-owned business located in Lewisburg, Pennsylvania. Tilo creates natural hardwood architectural millwork, mouldings, furniture, and cabinet components for home builders, contractors, and other manufacturers.
During its early years, Tilo used separate accounting and database software programs to manage the business. However, as the company grew, it quickly outstripped the capabilities of its patchwork system. Upon the recommendation of a customer, Tilo arranged demos of ERP software and quickly choose Global Shop Solutions. And the impact to their business was immediate.
32% Increase in Shop Floor Efficiency
Tilo uses many different species of wood of varying thicknesses and lengths to make their parts. The ability to group raw materials using op codes in Global Shop Solutions had an immediate and significant impact on Tilo’s shop floor efficiencies. Rather than cutting the wood individually for each job, saw operators use the op codes to group jobs that use woods of the same species, thickness, and length. They bring in a pack of lumber, cut all the orders that require that raw specific material, and then use move tickets to assign them to the appropriate jobs. They use the same process when milling like-profile pieces through the molder.
And in the increased predictability of scheduling available through Global Shop Solutions, Tim Yoder, Owner of Tilo Industries, estimates a 32% improvement in shop floor efficiency.
Prior to implementing the software, scheduling was all done on paper, requiring us to manually sort through all the jobs and due dates and try to pull it all together. Now that we do flex scheduling with everything driven by due dates in the system, our workflow has dramatically improved.
Tim Yoder, Owner at Tilo Industries
Precision Job Costing – On Every Job
With Tilo’s old system, job costing tended to be a hit-or-miss process, with workers usually clocking in just for the day rather than logging on or off jobs. As a result, supervisors struggled to calculate overhead and labor costs for each job. Using Global Shop Solutions to accurately capture operational time and material usage on jobs and sequences has significantly improved costing accuracy.
Near Perfect On-Time Delivery
The ability to track every job step by step – in real time – has enabled Tilo to improve on-time delivery from a pedestrian 75% to the current high of 98%.
As long as the job information is properly entered into the system, Global Shop Solutions provides the visibility of data needed to keep jobs on track.
“Every job has time and materials estimates,” explains Tilo Industries’ Plant Operations Manager, Linus Yoder. “As we enter new jobs into the system, we can see ahead of time if we will encounter any constraints, overbook any workcenters, or do anything else that might cause a job to be late.”
Poised for Robust Growth
Growing a business requires accurate, trustworthy data that leads to intelligent business decisions. Tim gathers data from the Business Intelligence application to make decisions that impact the long-term growth of the business.
Armed with this data, management can now discern what type of customers and market segments are driving Tilo’s growth, allowing them to position the company to focus on value-added rather than commodity markets.
Download the full case study to read about all the ways that Tilo Industries has improved their business with ERP software.