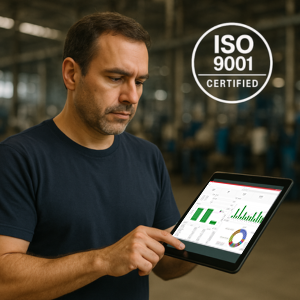
ISO 9001 doesn’t just signal quality – it demands it. For manufacturers, combining this certification with a robust ERP system turns a compliance challenge into a competitive edge.
Who doesn’t love a seal of approval? Or when something is sealed with a kiss? Does the ISO 9001 certification seal give you the same good feelings? It should! The incredible quality management certification standard earned by over 1.3 million organizations can feel like an arduous journey – but when you finally get that seal of approval, your performance, customer expectations and quality make you feel proud. It validates a commitment to quality, consistent operations and customer satisfaction.
And in many industries, it has become a requirement to acquiring certain contracts.
“Using an ERP system in ISO 9001 implementation helps ensure you’re not just compliant – you’re consistent, traceable and efficient.”
Dusty Alexander, President & CEO, Global Shop Solutions
The Business Case for ISO 9001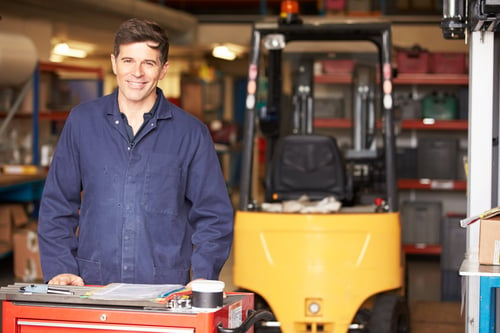
The benefits and advantages of ISO 9001 certification are many, including:
- Improved quality and consistency
- Increased efficiency and productivity that reduce waste
- Access to new customers and markets
- Enhanced customer satisfaction
- Reliable quality products that lead to positive word-of-mouth referrals
- Better risk management that reduces costly errors or delays
- Improved employee morale and engagement
- Enhanced company reputation and credibility
But what many don’t know is the secret to a simpler certification: ERP software. The best manufacturers utilize their ERP systems to support every aspect of the certification process.
Get the Certification Job Done Better
To make the certification process straightforward, the ERP system and ISO process need to be managed as a partnership. Manufacturers that combined ERP implementation with ISO 9001 certification reported a 25–50% reduction in the overall certification timeline.
ISO 9001 provides all the regulations, requirements and standards; ERP tracks all the data, organizes it and digitally transfers it to ISO 9001 for the certification process.
ERP uses many capabilities, such as automating processes, remarkably accurate data tracking and enhancing data visibility, to show consistent quality and meet the standard requirements. Additionally, one of ERP’s indispensable tools for certification is the robust quality control application, which can manage every aspect of the quality process of a manufacturing shop. This application tracks defects as they occur, isolates quality information using multiple variables, helps manage scrap, processes cause and corrective action and satisfies maintaining ISO 9001 certifications.
With ERP, our customers frequently report faster audit prep times, fewer non-conformances and greater confidence during certification and recertification audits.
7 ERP Features that Simplify ISO 9001 Compliance
ERP systems functions improve efficiency and quality and are essential for consistent operations for ISO 9001 compliance.
- Quality Control. ERP directs quality control and compliance management by allowing manufacturers to integrate quality checks into their standard processes and meet defined standards at every stage.
- Real-Time Data and Reporting. ERP systems help by identifying process bottlenecks and proactively addressing production line issues as they occur.
- Full Traceability and Auditing. ERP links data to specific batches or production runs that simplify auditing, verification of processes and quality control measures.
- Standardized Inventory Management. Accurate, efficient inventory processes improve supply chain reliability and product consistency, helping meet ISO’s operational control requirements.
- Compliance Tracking. ERP systems can be the hub to monitor, manage and document compliance efforts, ensuring you adhere to regulations, policies and standards – reducing the risk of non-compliance.
- Robust Documentation. Real-time data tracking helps maintain accurate, up-to-date and version-controlled documentation demonstrating compliance with ISO 9001 standards.
- Continuous Improvement. ERP’s analytics provide key points for implementing quick process changes that show continuous improvement.
Simplify Recertification with ERP
Every three years ISO 9001 must be recertified, which often brings more scrutiny than the initial audit. The ERP Process Documentation & Training module (PDT) simplifies the recertification process by recording and documenting your processes. Using PDT, you can easily:
- Create and review new and standard operating procedures
- Eliminate paper process documentation
- Maintain the requirements for all quality certifications without bulky paper
- Automatically record all processes, tasks and programs to update any information
- Comply with requirements
- Train employees consistently and efficiently
Whether you’re pursuing ISO 9001 certification or completing recertification, ERP helps make both processes simpler and less time consuming. Ask any manufacturer about the value of an ERP and ISO 9001 partnership. They will tell you ERP can be just what you need to get and maintain the ISO certification that takes your business to a new level of quality, customer satisfaction and profitability – while giving you pride in your own seal of approval.