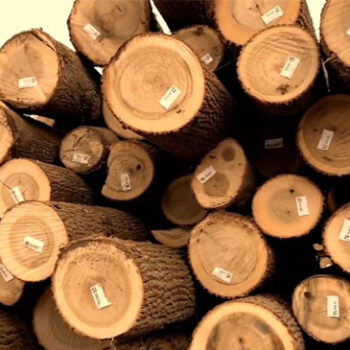
Based in Dundee, Ohio, Palettes by Winesburg is a family-owned, third-generation solid wood manufacturer. They hand select the best cherry, oak, maple, walnut, and hickory trees to produce dining room and bedroom furniture for users around the world .
Once the best lumber is selected, Palettes by Winesburg needed a way to automate the sorting and tracking of it as it moves through their shop. With Global Shop Solutions RFID (radio frequency identification) technology, Palettes by Winesburg has been able to turn their shop floor into a well-oiled, automated machine.
How Palettes by Winesburg Uses RFID
Once the raw lumber arrives at Palettes by Winesburg’s facility, it is sorted and placed out in the yard bin. An employee tallies up the number of logs received and enters specific information for each log into Global Shop Solutions ERP software. Data such as the part number, part description, grade of the wood, length of log, date received, etc. is all entered, and they print and staple an RFID label to each log.
That RFID label will then stay with the log throughout its journey into furniture. And its journey can be tracked on a simple Dashboard in their ERP system. No lost logs or missing wood – ever.
At each work station the RFID tag is scanned by an antenna mounted throughout the production process that reads the RFID label and updates the ERP software Dashboard. For example, when the raw lumber enters the warehouse, it is processed through the debarker and the RFID tag is scanned. Once the log has been scanned, an employee completes a bin to bin transfer and the information is automatically updated on the Dashboard. No mobile activity or human interaction required.
The second the tag is printed, Palettes by Winesburg employees are able to view all of the information through a Dashboard. This Dashboard is in real-time and allows them to print additional labels, issue the material to a job, and track lumber as it moves through the shop floor.
The RFID tag is read, logs are weighed and assigned to a work order.
From the debarker, the lumber is then pushed through a conveyor belt to the next station where the log’s RFID label is scanned again, and its quality is assessed and evaluated. This process allows for the RFID readers to tell the system if the log is fit or kicked out for quality and it automatically separates the raw lumber accordingly.
All logs that pass quality inspection are scanned and each log is weighed. Based on the quality, weight, and description the log is automatically assigned to a job and then sent via a conveyor belt to the saw process. This system automation eliminates the need for a human to assign jobs and process the log.
After being sawed the lumber then is sanded down and set to be crafted into beautiful fine furniture.
Want to See this Process in Action?
Interested in trying RFID at your manufacturing business? You can learn more here.