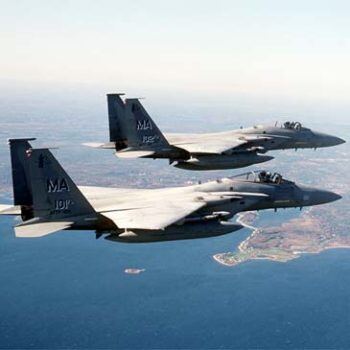
The thinking that enterprise resource planning software is strictly beneficial to the industrial sector isn’t uncommon. Manufacturing companies have long been looking for ways to generate more bottom-line revenue by eliminating waste and inefficiency and making customer satisfaction the highest priority. Lean practices have been the focus of organizations operating in the industrial sector for quite some time and ERP software adoption has increased as a result.
However, in a recent article from Defense Systems, it seems that companies with manufacturing interests aren’t the only ones leveraging the power of ERP software. The U.S. government is as well.
The website wrote that the U.S. Air Force is nearing completion on a large ERP implementation project that will move the defense agency from an organization that relies on multiple ERP systems into one, centralized database. The Defense Enterprise Accounting Management System is a small portion of a larger initiative called the Financial Improvement and Audit Readiness Plan.
DEAMS was launched more than a decade ago and was expected to be completed using a budget of $1.1 billion. However, in the 11 years that has passed since, the cost of the project has doubled to $2.2 billion. 2014 was originally the target year for completion. However, after receiving backlash due to flaws in the software code and failure to conduct a comprehensive risk analysis by federal agencies, such as the Department of Defense Inspector General and the Government Accountability Office, the Air Force is expected to have the system in place and fully operational by 2017.
McConnell Air Force Base in Kansas, Scott Air Force Base in Illinois, Joint Base Lewis-McChord in Washington and the Defense Finance Accounting Service were early adopters of the new ERP system where it is currently operational. However, the end goal of the DEAMS project is to have the system implemented at U.S. Air Force bases across the globe.
However, the challenges faced by the defense organization with respect to installation and deployment, are not that uncommon from those seen by manufacturing agencies in the corporate business sector. ERP implementation is both a time consuming and lengthy process. This can at times can become challenging and a source of frustration. Still, with proper planning and foresight, inherent hurdles can be cleared easily and with minimal effect on the project as a whole.
Avoiding common pitfalls during an ERP installation
Industrial Distribution offered several helpful suggestions for any organization considering making enterprise resource planning software a part of their operations. One of the best pieces of advice offered by the website is to develop an understanding of best practices within a particular industry and how an ERP solution can help address them.
This can be related to any number of areas such as customer relationship management, supply chain and logistics practices and other common business areas. Another suggestion is developing a vision for how the system should work once it has been fully installed and deployed. Understanding how information should flow between business units or departments and the type of data that needs to be shared by these separate entities will all help to map out the best way to ensure that things go without a hitch and ready to be used from the go-live date.
ERP software can benefit organizations tremendously, and this should be the mindset in the face of any challenges related to installation. As long as the positives related to the implementation of the system are kept at the forefront and remain the focus from the beginning stages of the project to the end, then the separate installation steps will be much easier to manage.