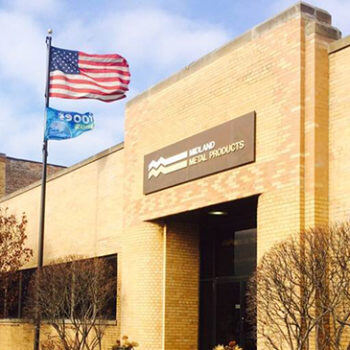
Midland Metal Products is a fourth-generation, family-owned and operated fabricator of sheet metal, wire, and tubing. Founded in the 1920s, the company has been serving the point-of-purchase display industry for 95 years. Located in Chicago, the firm’s 100,000 square feet production facility contains a collection of precision machining technologies, including laser, CNC, and robotics.
Over the years, Midland Metal Products has earned a reputation for quality products and exceptional customer service. With Global Shop Solutions ERP Software, they were able to add on-time delivery of their customized and specialized products to that reputation.
Simple Manufacturing
With cutting-edge ERP software, Midland Metal Products now can easily determine employee’s pay. They used to track all labor hours and pay by hand. Now it’s done automatically.
Because employees use Shop Floor Data Collection stations to log on and off jobs, Global Shop Solutions automates the entire process. We no longer have to manually track how many pieces our workers make, and it greatly simplifies our payroll process.
Jamie Brezinski, Director of IT at Midland Metal Products
Reporting and Real-Time Data Working Together
At Midland Metal Products, every job is a custom job that can range from fairly simple to complex. Their customers may come into the shop with their own design, but most likely, the customer makes use of a design and engineering team. This means Midland Metal Products needs to work efficiently to keep the shop humming and customers satisfied.
Brezinski says, “With Global Shop Solutions, we can pull up data while the job is running and make decisions in real time that affect the outcome of the job.”
No Islands at Midland Metal Products
Midland Metal Products has worked hard to teach their employees that when everyone works in unison, coupled with real-time ERP data, the sky is the limit.
“When people understand that no one is an island unto themselves, they also become more conscious of the data integrity. They know that they have to put in the correct number of counts or the packing list can’t be created. They know that they have to receive incoming materials correctly or we can’t pay our vendors. Having that kind of transparency throughout the system has a huge impact on the data integrity,” says Brezinski.
If you’d like to read the full case study, you can download it here.