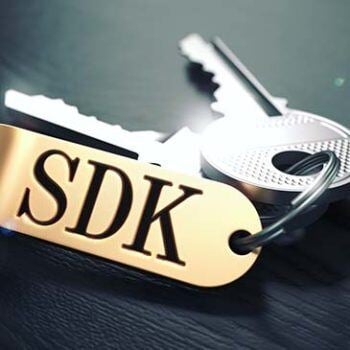
We offer over 80 training events, covering over 225 calendar days each year. One our most popular training being our ERP Boot Camp held at our headquarters twice a month. Taught by our ERP experts, our ERP Boot Camp is free to any customer and is the best place to learn the core aspects of the system and to train your mind on how to simplify your manufacturing.
Each class we ask our customers, “What are you manually doing in your business?” Inevitably the answer is hundreds of things and our goal is to get that data into our ERP system and automate your business. This automation accomplishes two things. 1) Excel (or other like pieces of software) are not a good place to store data. They are good tools to manipulate data, but not good tools to store data. If this is you then pick up the phone now as we can change your business immediately. You need a system that can store, push, pull, and pass information between applications to give you the best information to make smart decisions about your manufacturing. 2) You hire human capital with the expectation that they will think intellectually, process information smartly, and make critical decisions. The more human capital you have pushing pencils and doing the same routine over and over, the more damage you are doing to your business. Your human capital needs to be making decisions based on data being input and organized by the ERP system, not just inputting data.
Global Shop Solutions is one of the only ERP software systems on the market that offers a software development kit (SDK) to its customer base. The SDK allows a customer to build and modify reports or applications on top of the core system and has been one of the critical reasons for our success in helping manufacturers automate their business. For example, we have a great award winning customer that builds large dies and tools for the aerospace industry. Due to the short time requirements put on them by their customers, it was very difficult for them to build detailed bill of materials (BOM) and routers.
For years they were using a custom developed excel spreadsheet to manage customer requirements until Global Shop Solutions came along. Now, for various reasons, they still want to use this custom developed spreadsheet but were looking to integrate this with an ERP software system. Using Global Shop Solutions’ GAB SDK, our research & development team was able to build an integration that seamlessly passes the data into their Global Shop Solutions ERP software. This integration saves this aerospace customer about one hour per job and in busy months they can complete over 300 jobs per month for a total savings of 2,000 – 3,000 hours per year, or for most companies about 1.5 full-time employees!
This is a great example of why an integrated software system with the flexibility of a software development kit combined with a direct business model where all design, development, programming, service, implementation, consulting, and sales is provided by employees with the same company name on their badge is so critical to being able to simplify your manufacturing.
Push the Sled blog is written by Dusty Alexander, President & CEO of Global Shop Solutions, because no matter how good you get (at physical fitness, running a manufacturing business or being an ERP user) you can always work harder, get better, and be humble.