1 min read
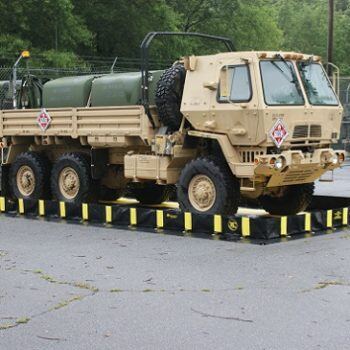
Founded in 1988, Basic Concepts designs and manufactures a variety of patented custom spill response and spill containment products for oil spill prevention, preparedness and response to prevent oil discharges to navigable waters and adjoining shorelines. Operating out of their 50,000-square foot facility in Anderson, South Carolina, Basic Concepts provides portable secondary containment solutions to more than two hundred military installations and hundreds of industrial sites around the globe.
Their berms are constructed to withstand the harshest of environmental conditions, including the sub-freezing temperatures of Antarctica, where scientists use the berms to protect the area’s fragile ecosystem. Basic Concepts’ berms have also been used to support U.S. troops in Iraq and Afghanistan.
To improve shop floor tracking, Basic Concepts installed five Shop Floor Data Collection (SFDC) systems throughout the shop floor. These allow operators to electronically clock in and out of jobs at their workstations, as well as access routers, work orders and other information related to each job. The company also uses SFDC systems to track how long it takes to complete a particular order, which has resulted in a more attentive work force and contributed to lower labor costs.
“With Global Shop Solutions, when employees pick up that router and log in on the job, they know exactly how much time we’ve allotted for that particular operation,” says Russ Guffee, Vice President and General Manager for Basic Concepts. “This ability to hold people more accountable for their time has generated improved efficiencies and cost savings.”
To learn more about Basic Concepts, download their case study or any of our other case studies here.