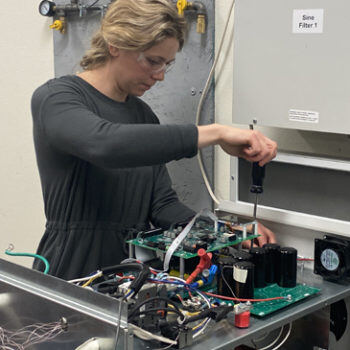
Phase Technologies is an OEM manufacturer of power electronics equipment for irrigation, water pumping, HVAC, CNC/machine shop, oil and gas, and other industrial applications. Phase Technologies started out in a garage of an electrical engineering professor, developing the world’s first digital phase converter. Since then the company has expanded into producing a complete line of variable frequency drives (VFDs).
Ownership recognized that a rapidly growing company that manufactures complex assemblies for rugged outdoor environments needs more than Excel spreadsheets and QuickBooks to manage the business. In 2010, Phase Technologies implemented Global Shop Solutions.
Make Any Product, Any Time
One of Phase Technologies’ biggest challenges comes from maintaining enough inventory to meet lead times expectations of three to 10 business days. With ERP software, the information they need to meet this challenge head on is right at their fingertips.
“I spend a lot of time in the Inventory Control module monitoring parts on hand, on order, and reorder points,” says Glenn Bailey, Production Manager at Phase Technologies. “In the past, we couldn’t tell how many of a certain part we used in a year because we didn’t have the data. Now it’s there with just a few clicks of the mouse.”
Taking Care of Business
In addition to keeping tabs on inventory, Bailey uses many different modules to perform a variety of shop tasks. In Shop Floor Control, he generates work orders to get jobs started and helps issue materials when needed. He also assists with Estimating, Routing and building BOMs, closing operational steps, and WIPing assemblies to finished goods. He uses the General Ledger to check on accounts payable and receivable and the Quality Control module when product quality issues arise.
Bailey also appreciates the ability to create tailored Crystal reports to handle certain situations. For example, sometimes closed orders don’t align with how many parts are actually in the bin. To address this disparity, Bailey created a Crystal report to identify when parts haven’t been issued to a work order.
Accurate Job Costing
Their ERP software has also improved a process critical to every manufacturing business – tracking the true costs of making each product.
“Our business keeps growing, but there’s a difference between growth and profitable growth. Thanks to the software, we definitely have a better understanding of our true costs.”
Genn Bailey, Production Manager at Phase Technologies
“Global Shop Solutions can do so many things for a manufacturing business, but it all comes down to how you put data into the system and how you get it out,” concludes Bailey. “It took us a while to set up and configure the system in order to do things the way we like to do them. But we’ve been using the system for 10 years and I can’t imagine doing what we do without it.”
To read more about Phase Technologies’ and the benefits they’ve received from ERP software, read the full case study.