1 min read
Medical Manufacturer Saves Thousands of Shop Floor Hours with Barcode Integration
Admin August 19, 2021
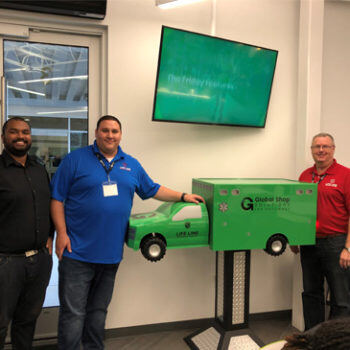
Life Line Emergency Vehicles manufactures high-quality custom ambulances and emergency vehicles. Headquartered in Sumner, IA, Life Line has spent 35 years building a reputation around remarkable customer service and exceptional quality and craftsmanship to ensure their customers can provide the best patient care possible.
Many manufacturers are expected to maintain consistent pricing despite often rising material costs. Brady Robbins, former Systems Administrator for Life Line, can attest to this fact.
“I recall one year that the cost of aluminum went up significantly, which would have resulted in a $1,000 increase in ambulances,” he says. “But, we had to find ways to lower our expenses in other areas to offset the increase to keep the cost level.”
Life Line faced a few challenges such as work orders in progress, job costing, and shop floor efficiency. They struggled to respond quickly enough to the data to hold shop workers accountable because data was often input manually after a job was completed. However, with a few simple adjustments to their processes and a new barcode scanning integration for their ERP, Life Line has been able to save over 30,000 shop floor labor hours a year.
A Simple Barcode Integration
Life Line implemented 15 workstations complete with computers, EMS barcode scanners, and dual-monitors placed at various locations throughout the shop floor so employees could see job-related data in real-time as a project was being worked on by scanning barcode labels throughout the life of the project.
“This enabled workers and managers to see work in progress, job costing estimates, and other key data points associated with their respective departments.”
Brady Robbins, former System Administrator at Life Line Emergency Vehicles
Initially, the integration garnered criticism from employees and staff that didn’t see the need. However, employees and managers started looking to the monitors regularly to see how their department was trending compared to other departments.
“One of the nice things about the displays is that they don’t just show rows of numbers, but they also incorporate color,” said Robbins. “So, if a job is falling behind, the row turns red, which enables a manager to spot it and work to correct the problem quickly.”
To learn more about integrations that can simplify your manufacturing, schedule a demo today.