1 min read
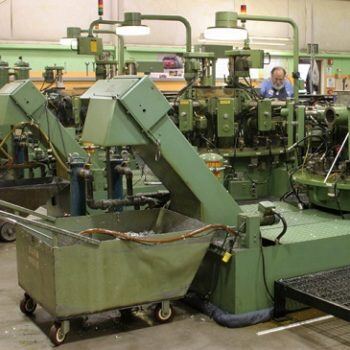
A family-owned company founded in 1949, Enoch Manufacturing designs and manufactures a wide range of precision machine parts for industries ranging from aerospace to sporting goods and clients ranging from Fortune 500 firms to emerging businesses. Located in Clackamas, Oregon, Enoch’s 48,000 square foot facility produces more than 3.5 million parts each month.
When Enoch purchased Global Shop Solutions ERP software, management decided to implement the software in bits and pieces rather than utilizing the full system. This included continued use of their manual scheduling system rather than Global Shop Solutions’ Advanced Planning & Scheduling (APS) software. The manual system, which consisted of metal boards with color-coded cards affixed to hanging tabs, proved too cumbersome to work well with Global Shop Solutions’ online work orders and routers. Enoch soon switched to an Excel spreadsheet system, which turned out to be less of an improvement than expected.
In 2007, a new CEO made it a priority to begin taking full advantage of Global Shop Solutions, including the APS application. Since switching to APS, Enoch has gone from a full-time scheduler to only needing two to three hours a day for the scheduling process. In addition, the process/manufacturing flow has become much more consistent and predictable. According to Rob Poyser, Director of Logistics for Enoch, “With Global Shop Solutions, we have complete visibility of how our primary processes drive our secondary processes, and can schedule our secondary machines accordingly.”
To learn more about Enoch Manufacturing, download their case study or any of our other case studies here.