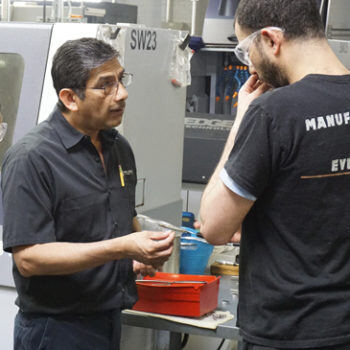
A certified Women-Owned Small Business, Pioneer Service has been making custom components for its customers, including many in the medical industry, for more than 30 years. Its medical products include parts for equipment essential to the battle against the COVID-19 virus, such as ventilators, respirators, and hospital beds.
When COVID-19 began overwhelming hospitals and first responders, many of Pioneer Service’s medical customers found themselves unable to meet the sudden surge in demand for these vital pieces of equipment. In addition, Pioneer Service began receiving inquiries about precision machined components for new equipment needed by hospitals and medical teams on the front lines.
In response, Pioneer Service immediately increased capacity so it could dedicate 70% of its facility to manufacturing medical parts, including new components for companies that make ventilators and respirators. Pioneer Service even began producing a new type of hospital bed system that makes it easier to move patients from one location to another.
“We had begun ramping up for strong growth before the onset of the pandemic. So we already had the people and equipment in place to increase production. The main issue was whether our suppliers could meet our need for raw materials. Fortunately, most of them have come through for us.”
Beth Swanson, Vice President of Marketing at Pioneer Service
As production shifted into high gear, another significant challenge reared its head – keeping a full crew when many employees have young children or elderly parents to take care of at home.
“COVID-19 has turned everyone’s life upside down, and we had to make some adjustments so employees can come to work every day,” says Swanson. “We designated a person to shop and run errands for employees. We’re bringing lunch in once a week. And we continue to look for other ways to reduce employees’ stress so they can focus on their jobs.”
As an ISO 9001 and AS9100 company, Pioneer Service makes a clean working environment a top priority. However, protecting against lethal germs has taken their cleaning protocols to a new level.
“We’re working hard to ensure our team members stay safe in the plant,” says Swanson. “We require employees to wash their hands when they arrive and leave work. We wipe down all machine surfaces between shifts. Everyone wears gloves on the job, and we don’t allow visitors in the building. The hardest part is staying six feet apart due to the collaborative nature of our work.”
“As a business, part of our mission includes being a leader for positive change in the world,” adds Swanson. “We place a high value on community outreach, and have a long history of helping whenever and wherever there’s a need. But we feel an extra level of commitment to the brave people all across the U.S. who are battling the virus. We need to stay well so we can help others recover.”
This is just one of our great customers who have risen to meet the challenge.