2 min read
Machine Shop Sees a 50% Reduction in Raw Materials Inventory in Just 6 Months with ERP Software
Admin August 20, 2020
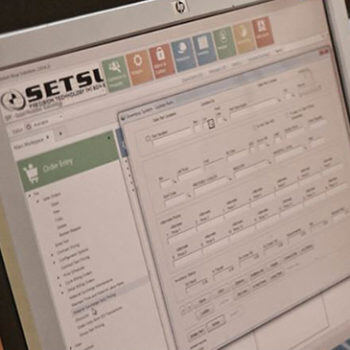
Setsu Precision Technology (M) Sdn Bhd is a leading precision engineering and machine shop in Malaysia, providing a full range of engineering services, including CAD/CAM, and surface cleaning and heat treatment processes.
Setsu shares many of the same challenges encountered by U.S. manufacturers: the need for real-time information, accurate inventory tracking, and the ability to efficiently schedule workflow through the shop floor. And like many U.S. manufacturers, Setsu found its solution in Global Shop Solutions ERP software.
50% Reduction in Inventory
In less than six months since implementation, Global Shop Solutions ERP software produced dramatic results for Setsu, starting with big improvements in their ability to manage inventory.
First, the ERP software helped to reduce the number of parts in inventory by eliminating the need for multiple numbers for the same part. It also enabled Setsu to consolidate multiple small orders of raw materials into larger bulk orders to realize substantial cost savings. And the “frequent use” inventory feature led to further cost savings by identifying which frequently used parts Setsu should keep in stock.
“Thanks to Global Shop Solutions, we no longer waste time waiting for frequently used parts to come in because we now keep them in stock. Everything else we order just-in-time. Within four months, we reduced our raw materials inventory by 50 percent!”
Suresh Vaithilingham, Owner at Setsu Precision Technology
Speeding Up the Information Flow
In today’s highly competitive manufacturing markets, the smooth flow of information can often make the difference between winning and losing jobs. Setsu uses Global Shop Solutions’ versatile Document Control software to speed up both internal and external communications, including vendor quotes.
To manage their large library of internal documents, Setsu uses another feature called Document Catalog. Here, they store preventive maintenance manuals, customer and material requisitions, and important documentation – all of which are instantly available with just a few clicks of the mouse.
Simplifying Manufacturing
Vaithilingam continues to be amazed at the noticeable improvements in all areas of the business.
Employees take far less time to get their work done. Productivity has improved. And with the Moveable Dispatch Chart, people no longer stand around wasting time because they don’t know what to do next. Recently, Setsu planned to do a job in 28 days but finished it in 23 – a firm testament to the ERP software’s ability to simplify production processes.
Setsu’s raw materials storage area is cleaner and more organized, making it easier for people to find what they need. The Quality Control application enables workers to identify the causes of defects in real time and take appropriate action. The CRM application speeds up customer response time. And thanks to the real-time barcoding feature, Setsu now packs and ships their finish goods much more efficiently. No longer does a part get shipped without an invoice or vice versa.
To learn more about how Setsu has benefited from ERP software, download their full case study.