1 min read
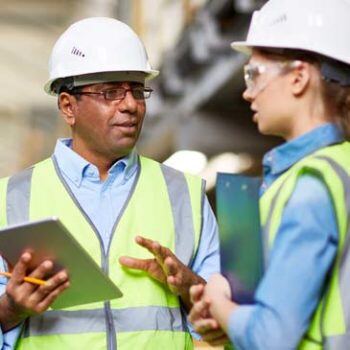
To compete globally, especially for North American or European manufacturers against markets with historically lower costs of labor such as Asia-Pacific, Latin and South America, and the emerging African labor market, labor costs must be kept to an absolute minimum.
This doesn’t mean fewer people; it means fewer wasteful minutes. Even as recent as five years ago for some, managers had to physically watch the shop floor to be sure work was getting done. This was helpful, but the freakonomics of it didn’t tell the manager if the person was efficient and doing what they were supposed to be doing. Performance was subjective.
This all changed when the manufacturing shop floor and management became objective. How did this happen? The introduction of software and technology making up the Shop Management and Shop Floor Data Collection modules of Global Shop Solutions enables move tickets; barcode scanners; RFID technology; clocking in and out of the facility and jobs; as well as speeds up setup times and work processes all made this happen. You can now measure performance, effectiveness, efficiency, and quality of each employee, team, or department.
Even better than that, the employee now has transparency to their performance and expectations. This is accomplished by leveraging real-time data on the shop floor with touch screen graphical user interfaces (GUIs). Know what your employees are doing as they are doing it. Call it fantasy football for your manufacturing business.