1 min read
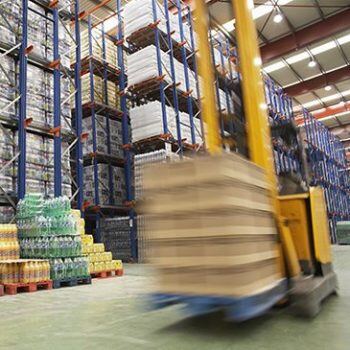
Many schedulers in the manufacturing industry work anywhere from 60 to 70 hours a week and still feel like they need another 20 or 30 hours to complete the job. From tracking and managing work orders to meeting deadlines, these individuals have a lot on their plates.
With ERP software, schedulers don’t need to stress anymore. ERP simplifies and automates the planning & scheduling process, taking the load off the management team. The program can handle delivery and billing as well as components of purchasing, inventory management, accounting and financial activities. All of these modules make the scheduler’s job easier and less time-consuming.
However, to take full advantage of the program, be sure to update the schedule as necessary, ERP Focus reported. Life goes on, so the schedule needs to adapt to real-life situations. Global Shop Solutions acknowledges this by offering small and mid-sized discrete manufacturers the opportunity to revise the schedule with ease. It only takes a couple clicks on the mouse to see how that rescheduling affects other jobs in the system.
What manufacturing companies value most about Global Shop Solutions is its “what-if” feature. Manufacturers can provide the software with a number of scenarios and find out the potential impact without making actual changes in the system.