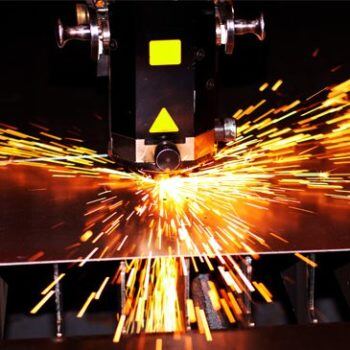
Operating a laser or plasma machine comes with challenges. That’s why we created our Nesting Interface software so that your ERP and nesting software have a customized back-and-forth exchange of information to simplify your shop floor production. Our nesting software partner SigmaNEST offers solutions to many of the challenges manufacturers face, helping your machine to achieve optimization and allowing operators to get jobs completed quicker and safer. Let’s look at the three ways you can improve your laser and plasma machines’ production on the shop floor:
- Part Quality: Bolt Hole Quality (BHQ) and Corner Loops
BHQ is a feature that is best suited for plasma machines and is not used for roundness correction, but rather reduces hole imperfections. It works with the advanced built-in features of your machine and with multiple controllers and systems to improve tapering and dings on holes at lead-ins/outs. BHQ will automatically set-up your lead-ins correctly, saving you time and wasted material from wrong cuts. Additionally, corner loops, primarily for plasma machines, allow you to maintain sharpness in a cut while keeping the machine running at an optimal speed. - Motion Optimization: Laser Destruct, Part Avoidance, Curvy Rapids
Laser Destruct is a programming technique, which makes systematic cuts to keep internal contours from tipping up and causing the laser head to crash. It cuts a large internal contour into smaller pieces that can easily fall through the slats of the machine bed. Additionally, using this technique eliminates the need to tab internal contours, preventing additional processes and extra manual labor, and allows operators to set up specific parameters around different size contours and limit where parameters are applied.Part avoidance is an advanced technique that creates an optimal head motion path, eliminating costly head raise time while avoiding previously cut toolpaths. Part avoidance allows the head to stay down over uncut material and minimizes the chance of crashing into tipped-up parts, saving time and preventing potential damage to the machine.Curvy rapids is a new feature that optimizes the rapid path. Laser machines are becoming increasingly fast, but sharp angles and turns can cause the machine to slow down. With curvy rapids, the machine instead curves around to get to the next cut, without slowing down, keeping the machine moving at an optimal speed. - Pierce Reduction: iPierce
A laser cutting torch generates a sudden and forceful concentration of energy initiating the cutting sequence, referred to as a pierce. Each pierce point takes a toll on the torch and eats away at your man hours, because the thicker the material the longer it takes. With iPierce, you can reduce the number of pierces the machine makes by turning on the feature in your system.
Interested in learning more on how you can optimize your laser and plasma machines? Watch the SigmaTEK Advanced Laser and Plasma Training webinar here.
Authored by SigmaNest, one of our industry partners.