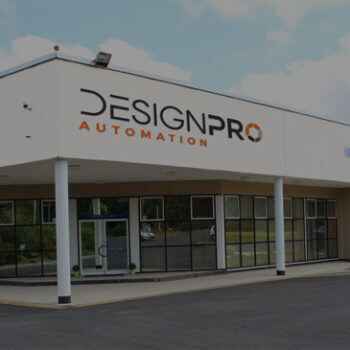
DesignPro Automation is headquartered in County Limerick, Ireland and is a leading provider of precision automation and machine building services and offers solutions anywhere from design, prototyping, installation, maintenance and more for automated robotic solutions.
As a young growing company, the need for an integrated ERP system to simplify manufacturing processes became paramount. Madeleine Collins, Quality Manager for DesignPro, led the ERP research, selection and implementation team, which resulted in going live with Global Shop Solutions.
Process Changes Drive Positive Change
DesignPro’s primary goal after going live with their new ERP system was to improve the speed and accuracy of data collection, starting with labor time. To ensure this outcome, the Global Shop Solutions implementation consultants worked closely with Collins to accurately migrate data from the company’s old systems and properly set up automated data collection processes in the new system. It didn’t take long to begin seeing significant results.
“Now that employees log their time directly into the system, processing labor hours takes a fraction of the time it used to. We can see the whole history of what people are doing at any given time. And, with the work orders and time clocks providing accurate live data, we have much better control over costing and pricing.”
Madeleine Collins, Quality Manager at DesignPro Automation
Upscaling Inventory and Purchasing
Purchasing and inventory processes have also made great strides in a very short time. The price of parts and materials DesignPro needs to build their products often fluctuates on purchase orders. Previously, design and purchasing personnel used data from a manual spreadsheet to get the best price. Now, purchasing data goes straight to the inventory module, so purchasers can see fluctuations in pricing and make purchasing decisions to get the lowest price.
Robust Dashboards
Collins uses a variety of screens and Dashboards to get a quick overview on the current status of employees, processes, jobs in progress and more. Her first task of the day involves making sure shop floor personnel are logged in. As the day goes on, she refers to the Labor Performance Dashboard to check the labor balancing status.
“Our goal is to have every direct worker average at least 80% direct labor hours per week,” says Collins. “The Dashboard reporting lets us know what employees are doing so we can accurately track direct versus indirect. Determining accurate labor costs has made our schedule more accurate.”
Superb Overseas Support
The combination of local support from Global Shop Solutions’ UK office and headquarters in the US played a key role in DesignPro’s purchasing decision. When technical issues arise, Collins can often resolve them by troubleshooting with the U.K. office. When a problem can’t be resolved, she opens a ticket and works with the US support team, receiving friendly, responsive service from far across the sea.
“Global Shop Solutions offers a great software package, but what stands out for me is the people and the support,” she says. “Everybody we’ve worked with in the UK and US has been amazing. The support team is very knowledgeable about the software and sincerely interested in helping us solve the problem.”
To learn more about DesignPro’s favorite ERP modules, check out their full case study.