3 min read
From Forest to Finished Product: ERP Software Improves Visibility and Tracking Capabilities for Walnut Creek Planing
Admin July 2, 2019
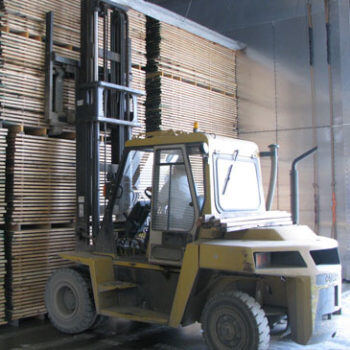
Walnut Creek Planing Ltd. (WCP) is a leading manufacturer of hardwood parts and components. From its 80,000 square foot facility in the rolling hills of Holmes County, OH, WCP provides high-quality hardwood components and finished goods for the door, stair, furniture, and butcher block industries.
The sophisticated tools in WCP’s facilities allow them to control the manufacturing process from forest to final product. This enables them to cut costs and operate more efficiently while ensuring that every product has the highest level of quality and craftsmanship. But WCP also uses another state-of-the-art tool to control workflow, cut costs and simplify the business – Global Shop Solutions ERP software.
Improved Shop Floor Visibility
Implementing Global Shop Solutions ERP software produced several immediate benefits for WCP, including reduced inventory costs and the ability to track jobs at every point in the production process. In particular, the Advanced Planning & Scheduling (APS) application helped to simplify scheduling by allowing the dispatch list to be automatically deployed – a huge time saver for workstations running many different jobs every day.
APS lets us schedule every job down to the exact minute. With their workflow automatically organized, the team leader at each workcenter simply selects the job off the top of the dispatch list. This makes it easy to identify which jobs have the highest priority, and the team leader just goes down the list in order.
Chad Wengerd, Information Technology Manager at Walnut Creek Planing Ltd.
Robust Manufacturing Inventory and Sales Tracking Capabilities
One of the best features of Global Shop Solutions ERP software is that it gives manufacturing companies the ability to track data in ways they always wanted to but were unable to do with their old systems. For WCP, this includes the ability to accurately track sales order history, customer quotes, and other key data.
In addition, Global Shop Solutions’ live inventory tracking has significantly simplified the movement of parts and materials throughout the busy warehouse.
“We used to have difficulty keeping track of where inventory was stored, especially in the middle of a demanding manufacturing process,” says Wengerd. “Our forklift drivers would go to pull a particular part only to find that it had already been used or moved to another location. This meant they had to spend time tracking it down in the warehouse or finding a material substitution that was not filling another requirement.”
Paperless Shop Floor
With the help of 18 Shop Floor Data Collection stations and GS Mobile, WCP has gone totally paperless on the shop floor.
The Shop Floor Data Collection stations allow operators to electronically log on and off jobs, which eliminates written time sheets. They automatically deliver work orders, routers and dispatch lists to each workstation. They provide critical job information by automatically linking drawings, job specs, and other documents through the Document Control™ application.
Customizable ERP Software
As head of IT, Wengerd appreciates Global Shop Solutions’ robust database architecture and reliable performance. He also likes the fact that it can be easily customized to fit WCP’s operating environment. Using the Global Application Builder (GAB), Wengerd has created a number of custom scripts and programs to make small manual processes more efficient.
With some assistance from a Global Shop Solutions ERP Consultant, Wengerd created a wireless ticket script. When team leaders on the floor clock in on an order, the system gives them an opportunity to create a pick ticket for the material on that order. If they choose to create a pick ticket, it identifies the amount of material they will need, which workcenter is requiring the material, and where it is stored in inventory in the warehouse. The operator identifies the forklift responsible for their workcenter, hits the print button, and prints the ticket to the wireless label printer on that forklift. The forklift driver instantly has the ticket in hand, and can pull and deliver the material to the workstation in a matter of minutes.
“I can’t tell you how much the wireless pick ticket has streamlined our workflow,” says Wengerd. “It was a real home run for us!”
A Powerful Competitive Tool
At WCP, enthusiasm for Global Shop Solutions ERP software extends beyond the shop floor and into the administrative offices, where the Customer Relationship Management (CRM) application is a big hit with office personnel.
When a customer calls in, customer service reps can access the customer’s entire company information -including contact information, sales order history, work order history, and open work orders – with only a few keystrokes. They can instantly let customers know the status of their order(s), including up-to-the-minute estimates for completion and shipping.
Read Walnut Creek Planing’s case study to learn more about ERP software made a difference in their business.