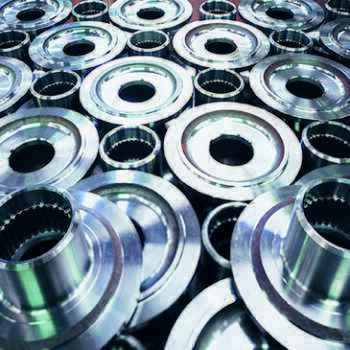
When implementing ERP software into your manufacturing business, one of the distinct features that often comes with it is production scheduling. Global Shop Solutions emphasizes that feature in their line of ERP products. Differing from previous paper methods, scheduling in ERP software automates the process significantly, cutting down on a lot of backtracking and miscommunication on the production floor. It also presents ways of improving customer service simply by managing projects more effectively, with the ability to expedite orders if necessary. Improving efficiency is something you can expect with ERP production scheduling, especially with our software.
One of the key elements of efficiency in an ERP production schedule is simple data entry. When a new work order came in before, you would have to notify everyone involved in production, either in person, or through middlemen that might miss important order details or just fail to notify the right people. Any of these situations would cause a break in the production. Now, with data entry, all you would have to do is input the work order once, and everyone involved in the manufacturing process of your products will know about it and adjust accordingly.
Another key feature for any ERP software is planning for the inevitable change of plans, whether it’s a new order that has priority, a customer suddenly demanding their order be expedited, or production abruptly halts because of a quality control issue. Handling these emergencies is pivotal to maintaining a steady level of operations, and production schedulers need to plan accordingly.
Richard Barker of ERP Focus notes that 10 percent of all manufacturing comes down to these issues, and that “In those cases, the production scheduling system needs to recognize that not all orders are created equal and allow for efficient flexibility.”
A core component of our manufacturing software is planning for those inevitable situations. If an order comes in that needs to be expedited, it can be rescheduled through an easy process. In doing so, you can determine the impact of this rescheduling on all other orders currently being processed ahead of time. In the event of a breakdown in production, finite scheduling that utilizes capacity to determine when orders are completed will prove useful in easing customer fears that their order will never come. By having such components in place, you can maximize the efficiency of your operation in the event of sudden changes.
In determining the quality of ERP software, focusing on efficiency is critical, and production scheduling can play a major role in establishing that focus.