2 min read
Becker Electronics Hits a Home Run with Improved Workflow and 99% On-Time Delivery from ERP Software
Admin June 26, 2019
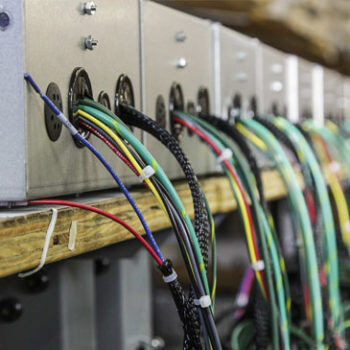
Becker Electronics, Inc. is an electronics manufacturer, specializing in custom cable assemblies, harnesses, and mechanical assembly services headquartered in Ronkonkoma, NY. They wanted to improve their on-time delivery, simplify their manufacturing scheduling capabilities and drive down labor costs.
Until recently, Becker Electronics managed production with an outdated ERP system that did not allow the company to maintain an organized and coherent production schedule. After a lengthy research process that involved close scrutiny of several different ERP vendors, senior management decided to upgrade to Global Shop Solutions.
We selected Global Shop Solutions for several reasons. The price fit our budget, and we liked the fact that we got a complete system rather than having to buy different applications and cobble them together.
David Sosnow, President at Becker Electronics, Inc.
Simplifying Manufacturing Scheduling
Sosnow’s first priority involved revamping the production scheduling process. To improve scheduling, Becker Electronics uses the powerful Advanced Planning and Scheduling (APS) application.
Planners use the reports available in APS to drive the scheduling process. The reports identify how much time is available for each workcenter and when jobs are due by the day, week and month. Instead of using an “up next” approach, schedulers use the data to determine when and where to schedule jobs. They also use APS to assign priority codes to each job, and create location and material flow codes that make it easier to track workflow through the shop floor.
“Prior to implementing Global Shop Solutions, we used to run behind schedule on almost every job,” says Sosnow. “Now we almost never fall behind. And if we do, we can look in APS and it will tell us why.”
50% Increase in On-Time Delivery
Thanks to Global Shop Solutions ERP software, Becker Electronics’ on-time delivery rate has nearly doubled – from an average of 50% to a consistent 99%. Sosnow attributes the remarkable increase to two key factors – the improvement in scheduling and production processes and the visibility of data throughout the system.
When he’s not managing production, Sosnow uses the software to keep tabs on the financial side of the business. Using the general ledger in the Financial application, he easily monitors cash flow, accounts payable and receivable, loan balances, and other key financial indicators.
Global Shop Solutions includes a complete accounting system that provides accurate data in real time. Having all the information at my fingertips makes closing the books at the end of the month a snap. I hit a couple of buttons and it’s done!
David Sosnow
Hitting a Home Run with Production Control
Global Shop Solutions ERP software is even helping Becker Electronics reduce excess paper. The company recently added 28 Shop Floor Data Collection stations on the shop floor. As a result, production workers can now electronically access drawings, work instructions, and other job-related documents right at their workstations – saving time and eliminating the need for paper in many processes.
“The software has turned out to be everything we hoped it would be and more,” says Sosnow, “but we’ve only scratched the surface of all it can do. We know we can gain a lot more efficiencies by using more of the system. And we know the product and the company is large enough to grow with us. I predict it will be a long time before we hit any limits within the software.”
Download Becker Electronics’ case study to learn all the ways that ERP software made their business more efficient.