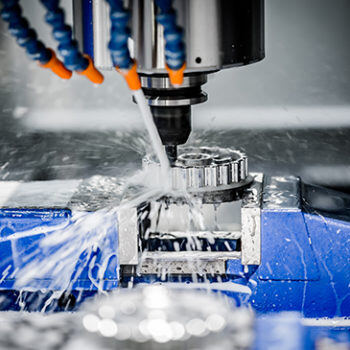
What good is scheduling and planning software that you pay for but is not being utilized or providing benefits to your manufacturing company? In that scenario, the software is costing you money instead of making you money. That is not how it is supposed work.
More than User-Friendly
One of the big selling points for Global Shop Solutions Advanced Planning & Scheduling (APS) is how user-friendly it is. It is easy to learn and easy to manipulate with drag-and-drop scheduling. Sometimes, “easy to use” means a software program has limited function. Limited function means it cannot do all the things you would like it to. This is not the case with APS. You get the best of both worlds with APS, a robust scheduling solution with amazing flexibility, along with an easy-to-learn user interface. It is like comparing a simple cell phone to a smartphone. A basic cell phone may seem simple to use, but it is limited on features. An intuitive smartphone will be both easy-to-use and loaded with features.
Intuitive Capacity Planning
So, why do so many manufacturers have scheduling software in their systems that is sitting idle? According to Erika Klein, Vice President of R&D at Global Shop Solutions, the main reason is that the software wasn’t adding any efficiency to their process. It provided a platform for entering data but didn’t give them the feedback necessary to make changes or improvements to their capacity planning. That is why our scheduling solution is called Advanced Planning & Scheduling. It doesn’t just show you the map ahead; it allows you to compare various scenarios, assisting you in better decision making.
When you see a bottleneck developing that could affect the on-time delivery of your orders, APS can help you determine the most cost-effective way to increase capacity and meet demand.
“Using ’what if’ scenarios, APS can show your production manager potential outcomes based on increasing manpower, increasing overtime hours or even purchasing an additional piece of equipment,” explains Klein.
“Finite scheduling is another feature of APS that sets it apart from the competition,” says Klein. The program doesn’t just schedule labor hours, materials, equipment and tools based on the needs of each project. The program works within the same parameters you do, understanding your limits on resources and your production priorities. You establish those parameters in the system, allowing it to quickly provide data that is both trustworthy and actionable. Jobs can be quickly rerouted or rescheduled with confidence.
Impressive Customer Service
When it comes to scheduling as it relates to customer service, the first thing that usually comes to mind for manufacturers is on-time delivery. A strong on-time delivery rate is critical to your customer service reputation, but Global Shop Solutions APS provides even more for your customers to rave about. Since your APS application is an integrated part of your Global Shop Solutions ERP software, customer service representatives have real-time access to jobs in production. When a customer asks for a progress update, the rep can give an answer immediately with total confidence and instant access right from their desktop customer screen.
Flexible and Accurate Estimating and Quotes
When your customer asks how much it would cost to make changes to an order, APS can run the ‘what if’ scenarios for multiple change options to give a true estimate of the increase or decrease on both production elements and delivery date. You can provide an accurate quote very quickly without the uncertainty of guesswork on the hours, costs or timeline. The APS data feeds into your Global Shop Solutions Shop Management and Project Management applications to allow analysis of estimated versus actual, providing new data for reaching lean manufacturing goals.
Designed to Save Time and Money
When your production flow has a sudden spike, either up or down, adjusting your use of resources appropriately is critical to maintaining profitability. “APS allows manufacturers to avoid the extra costs, short order fees from vendors or expedited shipping costs,” Klein shares. In-house, overtime labor costs can also be kept to a minimum and downtime for production slowdowns avoided. As with all the Global Shop Solutions ERP software applications for manufacturers, APS is designed to deliver a significant return on your investment. Which is why it is the scheduling software that manufacturers don’t just buy, they use.